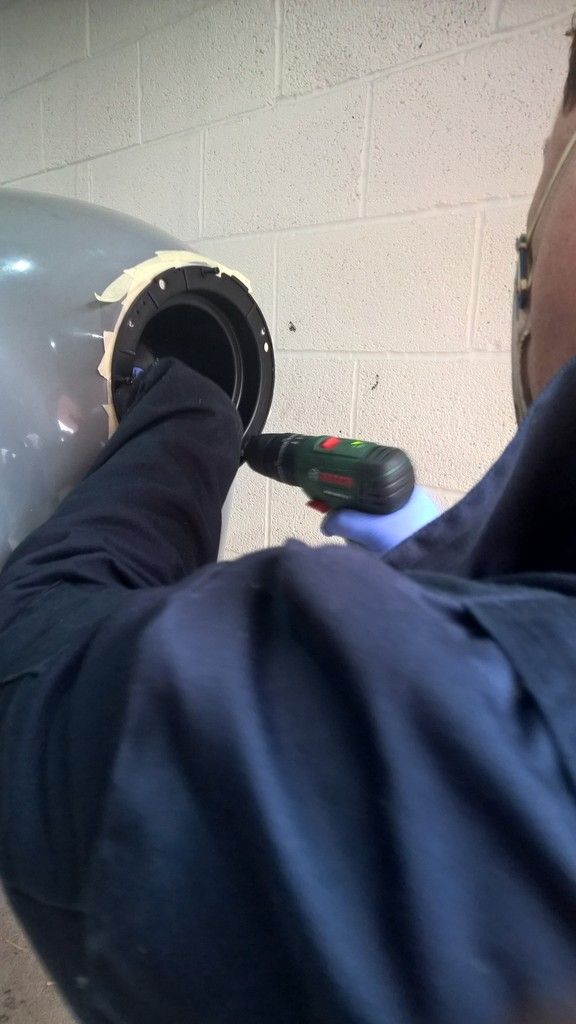
First make a template of the rubber seal on the headlights and drill the adjuster pin holes top and left. These need to be 8mm for the pins to fit through (start small and then open up the hole and don't forget safety mask as you're drilling fibre glass).
Remove the inner chrome mounting plate from the plastic bowl.
Next place the seal onto the plastic bowl and offer up into position. Drill at 3.5mm the fixing holes and then use No.10 self tapping 3/4" or 1" screws to fix it into position.
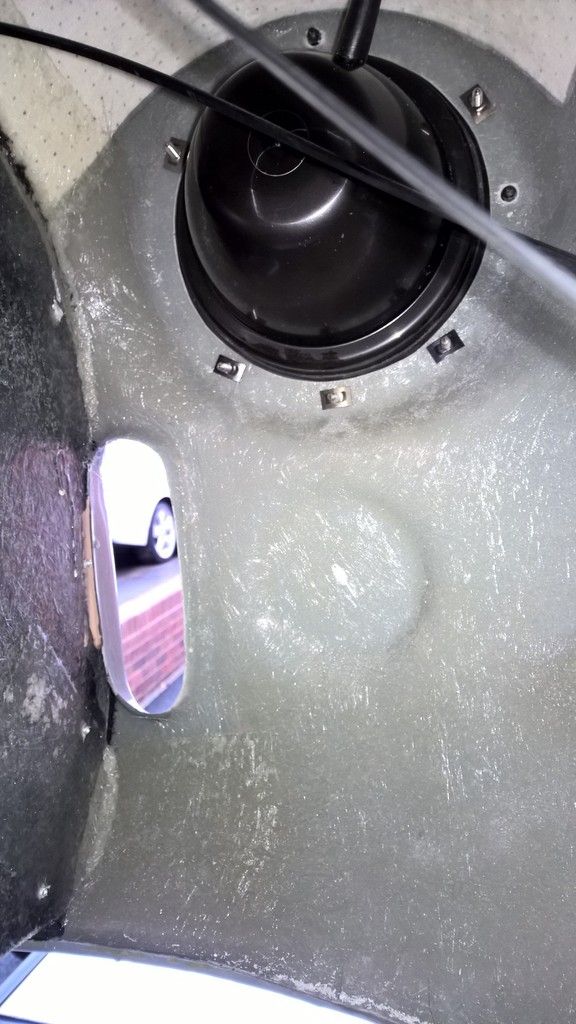
Push into place the small rubber grommet for the wiring to enter through inside the bowl. The wiring will be left for now and I'll come back to it when I do the main loom.
Now attach the headlight to the inner chrome mounting plate, ensuring you have the correct orientation of the headlight so that when you put the mounting plate onto the bowl the headlight remains the correct way up. The headlight simply secures onto the mounting plate with three retaining clips. Loosening two of these and removing the third should be enough to fix in the light.
The mounting plate secures onto the bowl by hooking into place on the two adjuster pins and securing with the retaining screw.
Ensure you have a small retaining clip on the square flat plastic plate as shown in the picture. These were missing from mine when I received them and S&J had to send them separately.
Place the chrome outer ring into position ensuring it lines up with the retaining screw holes (just off centre bottom right) and that it is hooked over the two plastic rims top left and top right. Insert retaining screw.
NOTE: the other hole in the outer rim is a drain hole.
Onto the indicators.
Locate the centre of the moulded area of the indicators. I measured this to be 4.25m radius.
Drill a pilot hole at around 3-5mm and then use a circular cutter to open the hole wide enough to fit the light into position.
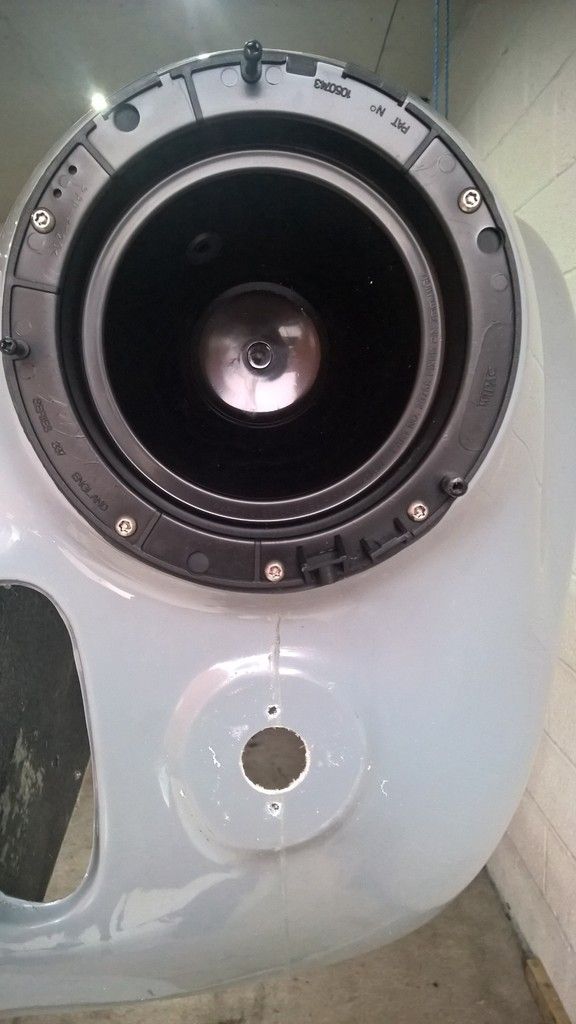
Then just repeat on the other side of the car.
For the eagle eyed - you'll see me daughter who was helping "photo bombing" me.
I'm pleased with the P700's and whilst I wait for the water pump I'll move onto the side repeaters next.