All I had to do was bolt the body down and arrange for it to go, then go on holiday and hope it was ready when I came back.
This time my mechanic friend was on holiday so couldn't transport the car. "No problem" I thought "AK can do it".
A phone call later and I realise their normal driver charges (at time of writing) £1.25 per mile which worked out at £255 each way!! an expensive addition to an already expensive order at AK. I needed another solution.
A quick Google search later and I come across AnyVan.Com. This is a simple site where you put where the car is going from and to and then companies can "bid" for your job. It started at £150 but within 20 minutes it was down to £123, less than half the price of the AK driver. The company I went with is based in Ripley, West Yorkshire
Email: grimsalvage@hotmail.com
Once the pickup occurs I'll let readers know how it went.
So back to the prep,
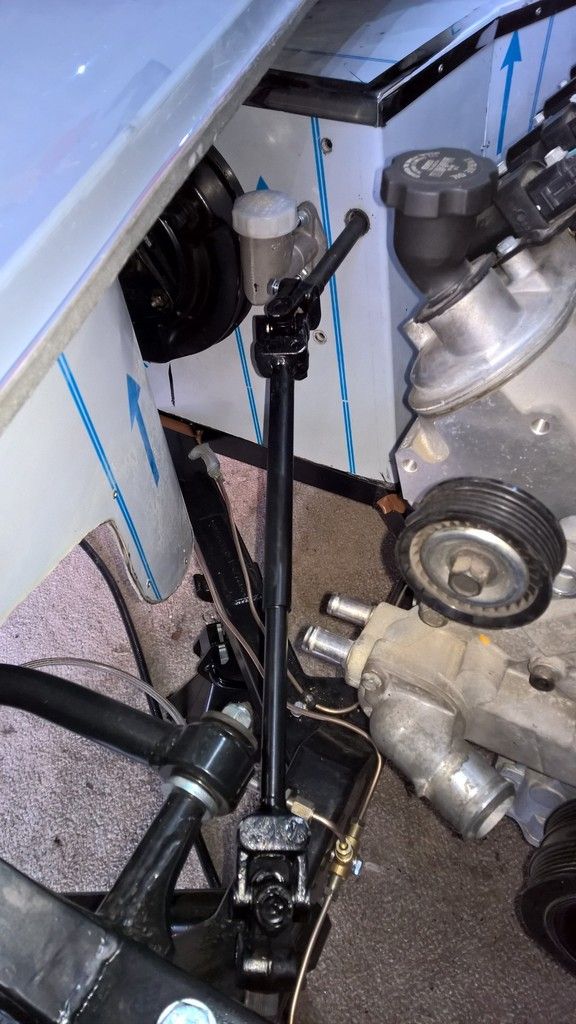

Everything has only been loosely fitted and will be removed later. One tip I have here is take the collapsible part of the column out and feed that through the hole in the bulkhead first, attach it to the AK provided steering rack extension (the black bar with 2 UJs) and then get someone to hold this still whilst slotting the column back onto it.
Another tip is pre-fit your brake pipes to the Servo and have connectors down near the chassis otherwise it is extremely difficult to connect them together.
Katie came out with Monroe to help bleed the brakes which took us a while as there was an air lock that just wouldn't clear. I finally managed to clear this just as I ran out of brake fluid to top up the reservoir.
All ready to go. The next time I post I'll have some side pipes :-)